

#Michael songster Patch
I bought a weed burning torch, got three 20 lb propane tanks filled and layed some concrete block on a barren patch of dirt and started burning wood. Still the extent of my knowledge of the process was pretty much limited to online video that should give anyone pause. I am not going to say skeptical because it made sense to me, charcoal is a very durable material, and the wood we planned on charring is a naturally weather and rot resistant wood, white oak. The treatment of the wood for the siding is something I haven’t ever done and I was still a little unsure of. steel panels completed across the rear of the house and working up the bay And Wood But as hot as the metal got it wasn’t anything like burning the wood siding in mid-summer under the relentless sun we had this July. The material sitting in the sun would heat up to the point you couldn’t handle it without gloves and the sweat marks from forearms pressed against the sheets when they were installed rusted quickly to a deep purple. the steel trim pieces installed on the bay window using the abrasive blade to cut the steel siding panelsĮveryone who touched one of those panels would have preferred to have been doing it in some other month than July. The shears produced a cut nearly as straight without the sparks and noise of the abrasive blade. This was generally slow and hot work, we started using an abrasive blade on a circular saw to cut the panels, but moved to electric shears by the end.
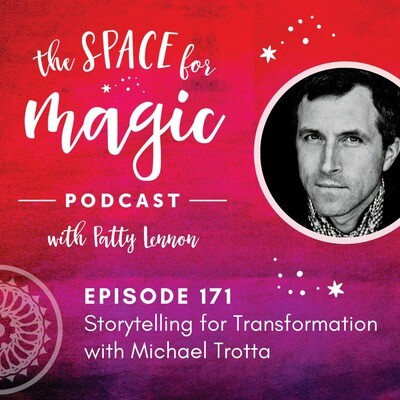
We installed the panels with an 1/8″ gap on all sides and at corners to provide more flexibility and since the steel is pretty thin (22 gauge) we tried to stretch the panels to provide tension in the interest of keeping them flat across the spaces between the battens.


The metal panels are screwed directly to the battens with #10 pan head screws. After that we installed a drip flashing at the base of the wall to provide a clean termination at the bottom of the metal panels.
#Michael songster install
With the windows and doors fully installed and weatherproofed our next step was to fabricate and install metal trim pieces to provide a transition between the flat metal panels and the exterior surface of the window frames. The first steel panel going on the house Steel Sheets of a weathering steel alloy for the bottom 8 feet, and durable wood, in our case white oak, for the rest of the wall surface. Early on we decided against brick, stone, or concrete, three things that can support and protect buildings for hundreds of years, pretty much leaving us with metal or durable wood for the exterior. That is a lot to ask of a building material. For this to work the exterior cladding has to cover and protect the house and be a material that can stay outside for a long time without deterioration. Obviously the siding plays a key role in achieving zero maintenance. No painting, no cleaning gutters, I guess we will clean windows from time to time, but since they all open in that ought to be easy.
#Michael songster drivers
If this data is unavailable or inaccurate and you own or represent this business, click here for more information on how you may be able to correct it.As I stated in an earlier post, maybe the first, one of the drivers for the design is to end up with a house that doesn’t require the standard maintenance of most houses. VIEW ADDITIONAL DATA Select from over 115 networks below to view available data about this business.
